Study Shows That Additive Manufacturing Reduces Emissions and Conserves Resources in Production for Fashion Footwear
AMGTA Lifecyle Research report highlights Stratasys's work with the Dyloan Bond Factory, a Pattern Group Company in the comparison of additive manufacturing vs. traditional production processes
Evidence revealed that a Stratasys PolyJet™ material jetting approach can cut CO2e emissions by 24.8% in comparison to injection molding and save 48% of stock material across the supply chain
Stratasys Ltd. (NASDAQ:SSYS) shared the results of a study commissioned by the Additive Manufacturer Green Trade Association (AMGTA), that demonstrates the environmental benefits of additive manufacturing for the fashion industry.
This press release features multimedia. View the full release here: https://www.businesswire.com/news/home/20231031433140/en/
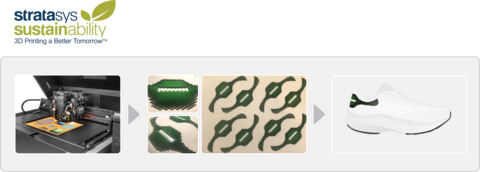
Demonstrating the additive manufacturing process flow in support of new research released this morning. (Graphic: Business Wire)
The report, "Comparative Analysis: 3D Material Jetting vs Traditional Methods for Designer Luxury Goods," presents results of a year-long collaboration between AMGTA, Stratasys, and the DYLOAN Bond Factory, a Pattern Group company - the first Italian hub of luxury fashion design and production. An executive summary can be found here.
The use case involved the modeling of the transition from traditional manufacturing methods to advanced Additive Manufacturing to create 16,000 units of a logo applique for 8,000 pairs of luxury designer shoes, printed on fabric, produced by the innovative Stratasys J850™ Fashion TechStyle™ printer. The analysis and results of the study revealed:
- Additive manufacturing print-to-textile production process cuts CO2e emissions by 24.8%, when compared with customer's traditional processes.
- When accounting for customer scope of production (16,000 printed logos, for 8,000 pairs of shoes), additive manufacturing can save almost one metric ton of CO2e.
- AM Print-to-textile saves 49.9% of stock material across the supply chain, reducing and streamlining transportation needs.
- AM print-to-textile with the J850™ TechStyle™ is a water-less process across the measured supply chain, potentially saving over 300,000 liters of water.
- Additive Manufacturing cuts electrical energy consumption by over 64%.
- Shift to AM reduces supply chain dependencies from 4 technologies to 1: with a single additive workflow (transportation and logistics are omitted for 3 processes).
- The shift optimizes production and logistical ‘stages' from 12 to 2.
The research was conducted by Reeves Insight, peer reviewed by ACAM Aachen Center for Additive Manufacturing GmbH.
"Producing sustainably is becoming increasingly crucial for designers in the world of luxury, and this is particularly relevant for Dyloan Bond Factory a Pattern Group Company as well," said Loreto Di Rienzo, R&D Director at the Pattern Group. "Stratasys' innovation in 3D printing with the TechStyle™ technology enables us to offer revolutionary capabilities by reducing waste, minimizing reliance on natural resources and optimizing the environmental impact of our entire supply chain."
Di Rienzo related to the AMGTA Lifecycle research, saying, "As revealed in the report on ‘Comparative Analysis: 3D Material Jetting vs Traditional Methods for Designer Luxury Goods' in which Stratasys and Dyloan Bond Factory collaborated, we can affirm and demonstrate that additive technology truly improves our environmental impact while expanding design freedom without compromising the quality of the end result."
The research project and its findings will be presented at FormNext, in Frankfurt Germany November 7-10, 2023, where Sherri Monroe, AMGTA Executive Director will present the body of work to the AM community and attendees across industries.
You are invited to join the session: Date: Tuesday, 07 November 2023 Time: 13:20 Stage: Application Stage, Hall 11.1
|
Sherri Monroe, Executive Director of the AMGTA commented, "We are pleased to issue the third body of research in a series of papers designed to reveal the environmental benefits of additive manufacturing adoption. We are committed to advancing the research and publication required to better understand the sustainable value of AM technologies as part of the manufacturing cycle for broad business cases. The Stratasys-Dyloan Bond Factory Fashion LifeCycle Analysis (LCA), assessing print-to-textile, is our first polymer undertaking. It delivers important data that supports the value of AM to impact one of the most polluting industries in the world."
This report showcases the Stratasys commitment to Mindful Manufacturing™, an approach that champions sustainability, efficiency, and innovation to 3D Print a Better Tomorrow™. Environmental concerns are paramount and can have a real impact on business results. Together with its customers, Stratasys is rethinking how things are made; redesigning processes, products and parts; and optimizing operations to the benefit of people and the planet.
"Our Mindful Manufacturing™ approach is a commitment to our customers," said Dr. Yoav Zeif, CEO at Stratasys. "By embracing sustainable practices and innovative AM technologies, we're working to reduce global carbon footprints – our own and our users. This study showcases how the adoption of our advanced AM offering empowers customers to deliver manufacturing solutions that improve their impact on the environment and at the same time deliver competitive advantage through innovation in production for design."
Stratasys invites its customers, partners, and those interested in 3D Printing a Better Tomorrow™ to join the Company on this journey towards more sustainable production. For more information about Stratasys and its Mindful Manufacturing™ commitment, please visit https://www.stratasys.com/en/about-us/sustainability/.
About Stratasys:
Stratasys is a global leader in additive manufacturing, delivering innovative 3D printing technology and solutions to a wide range of industries. With a strong commitment to sustainability, Stratasys is driving the transformation of manufacturing through Mindful Manufacturing practices and eco-friendly materials.
About Dyloan Bond Factory:
Dyloan Bond Factory, an Abruzzo-based company founded in 1987 with headquarters in Chieti and Villamagna (CH), deals responsibly with Research, Design, Prototyping, Sampling, Customization and Production of fabrics, semi-finished products, high-tech processes and finished garments.
The Dyloan Bond Factory comprises D-house laboratorio urbano, a responsible innovation laboratory with a pioneering approach to R&D, innovation and training, based in Milan.
In 2022 Dyloan Bond Factory joins the Pattern Group, forming the Innovation and Production Hub of Semi-finished Products, Accessories and Finished Garments and confirming its global positioning in the clothing, accessories, automotive and design sectors for the main luxury brands, also making use of the collaboration of the most cutting-edge technological partners.
About AMGTA:
The AMGTA was launched in 2019 to better understand and promote the environmental benefits of additive manufacturing across the global economy. AMGTA members represent the entirety of the manufacturing spectrum - from design and raw materials to end products and users - focused on innovating better, more sustainable, and financially advantageous products through best additive practices. www.amgta.org
View source version on businesswire.com: https://www.businesswire.com/news/home/20231031433140/en/